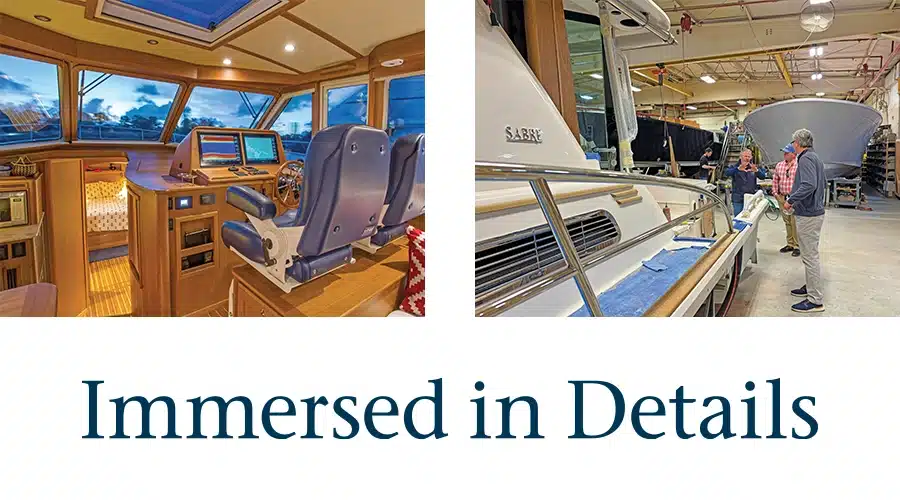
Behind the Scenes at Sabre and Back Cove Yachts
Representing the finest quality new boat brands requires continuing education and staying out front of all aspects of the boat building process. Constant learning and exposure to our brands and their factories allows Bluewater team members to become true experts and better serve our customers. In this spirit of purpose, several of our Downeast specialists recently completed tours of both the Sabre and Back Cove Yachts facilities in New England.
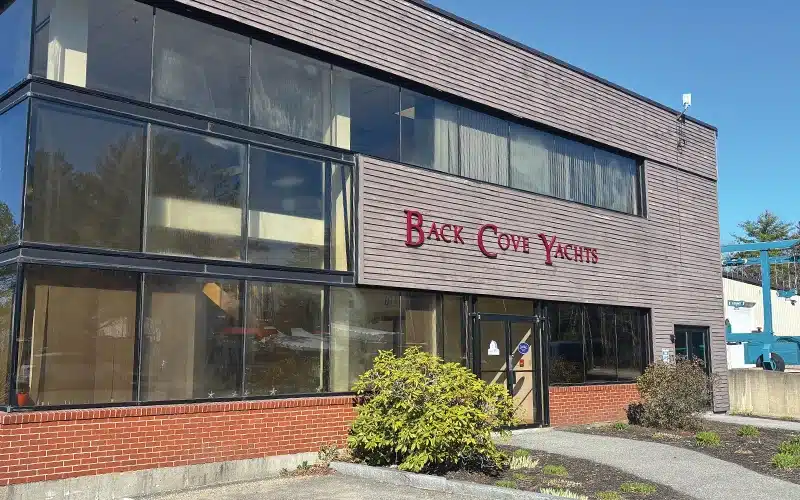
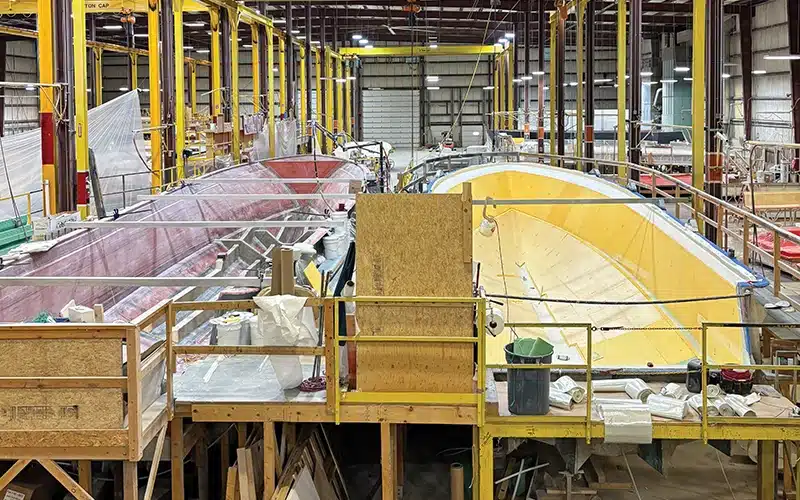
The trip began first thing on an April morning in Rockland, Maine, which is home to Back Cove’s massive 240,000 sq. ft. manufacturing facility. This location is responsible for all of the Back Cove models, the 34O, 39O, 372 and 41, as well as for the production of the Sabre 58 and the hulls of the Sabre 48.
Arguably, no one embodies the pursuit of continuing education more than Bluewater Sales Professional Mark Connors, who has been representing fine motoryacht brands in Virginia Beach for over twenty years. “We had a fabulous trip to both the Sabre and Back Cove factories, and learned a lot about the two brands. Both facilities are impressive, but the sheer volume of the Back Cove facility is amazing,” says Mark.
The tour naturally began with fabrication of the hulls. National Sales Manager Jamie Bloomquist and Back Cove President Jason Constantine explained the precise process of spraying the gelcoat, layering the fiberglass and high quality coring, and finally pulling it all together through infusion. This is a modernized process involving vacuum sealing parts and injecting resin to create an even application and a stronger and more precise part. Unlike many boat builders, Back Cove and Sabre infuse not only large components like hulls, but also infuse nearly every fiberglass part that goes into their boats.
Turning attention to the shaping and design of the hull surfaces, Jamie and Jason also pointed out the Trailing Edge Lifting Surface on the 34O and 39O Back Cove hulls. These flattened surfaces on the aft portions help create lift, faster planing speeds, and more efficient performance for these newer outboard-powered models. Also of interest is their automated cutting system, which trims each piece of fiberglass to the exact size needed for each part: reducing waste and expenses while increasing efficiency and value.
After seeing the Back Cove hulls, the Bluewater team visited the lower level of the facility, where the Sabre 58 and 48 models are brought to life. Although most of the Sabre line is built at a separate facility in Raymond, Maine, the Back Cove facility is used for the larger boats because of their larger footprint and closer proximity to the coast.
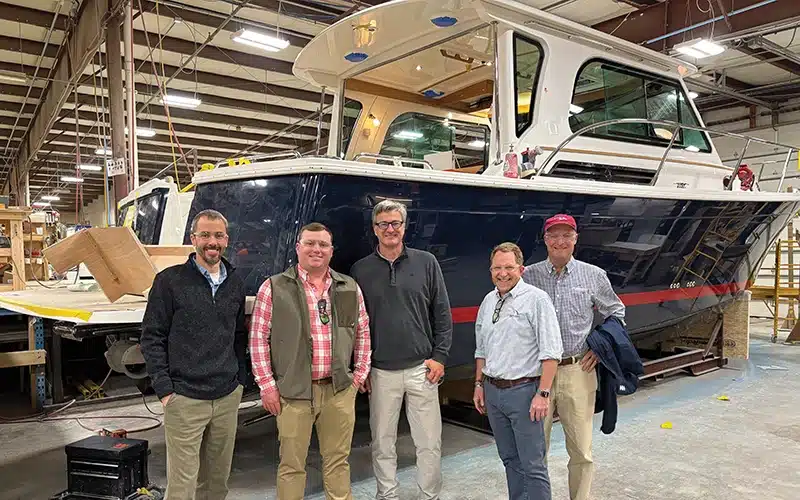
Shifting to Sabre
Departing the Back Cove facility, the Bluewater team then traveled two hours away to the Sabre Yachts campus in Raymond, Maine. This visit began in the original Sabre building, which has been running for more than 50 years; starting with the original Sabre 28 sailboats that initially ushered in the brand. This building has stood the test of time and vast changes in the marketplace—being utilized first as Sabre crafted their world-renowned sailboats, then introduced their first flybridge powerboat, and are now manufacturing some of the finest motor yachts on the market. This space is now used to produce the company’s two newest models, the Sabre 45 and the Sabre 43, while the Sabre 48 line is constructed in a nearby building.
Glen Chaplin, who has been working with Sabre for over 26 years, showed the Bluewater team around the original Sabre facility, starting with the hulls of the 43 and 45. Since Sabre and Back Cove share the same heritage, their build processes are very similar with the same fiberglass infusion used on the hulls and parts, but on a slightly larger scale for these bigger boats.
Perhaps the most impressive part of a visit to Sabre is how much woodwork is incorporated into each boat, and how much detail goes into creating each piece of the boats. When stepping into a Sabre, you will notice that there is an enormous amount of wood, including cabinets, window trim, tables, decks, bulkheads, trim, and more. Each one of these parts has to be cut, shaped, and stained so that the assembly team can put every boat together in exactly the same way. The amount of pieces is surely overwhelming, but the experienced team at Sabre has the organization and processes in place to build and perfect approximately fifty boats each year.
As the team continued through the building, they witnessed the evolution of the 45 and the 43 from bare hulls to fully completed yachts on the production line. First, the hulls are moved to the line and are outfitted with the engines, mechanical components, and electrical wiring. Then the lower interior accommodations are built before being topped with the deck and house. One unique technique of both brands is that the transoms are actually part of the deck mold, which allows the transom gate to be a solid piece instead of a patched junction between the deck and hull as seen in other production builders.
A similar build process is followed at the newer Sabre building just around the corner, where the Sabre 48 models are built, except for the hulls which arrive from the Rockland facility. This part of the trip was especially memorable because Bluewater’s own Sabre 48 was on the line preparing for delivery in the Summer. The Bluewater team was able to spend time going through the boat inside and out, inspecting it closely while the boat was moving down the line.
After the hull and deck are fastened together, the Sabre craftsmen add the remaining interior features before finishing the builds. Finally, the quality controllers go through the boats to make sure that everything is just right before going to the customer or dealer. The Sabre team also has dedicated “boat parents” who are employees responsible for keeping an eye on a specific boat from start to finish, to make sure that the boats receive all of the correct options and nothing is missed along the way. The result is a high level of quality control throughout each boat’s progress down the production line.
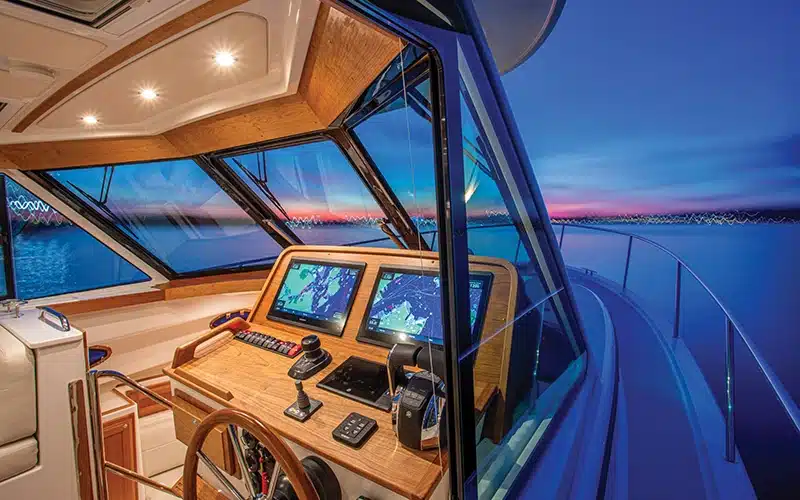
“There is an exactness to how each boat is built, which is very reassuring to witness, explains Mark.”